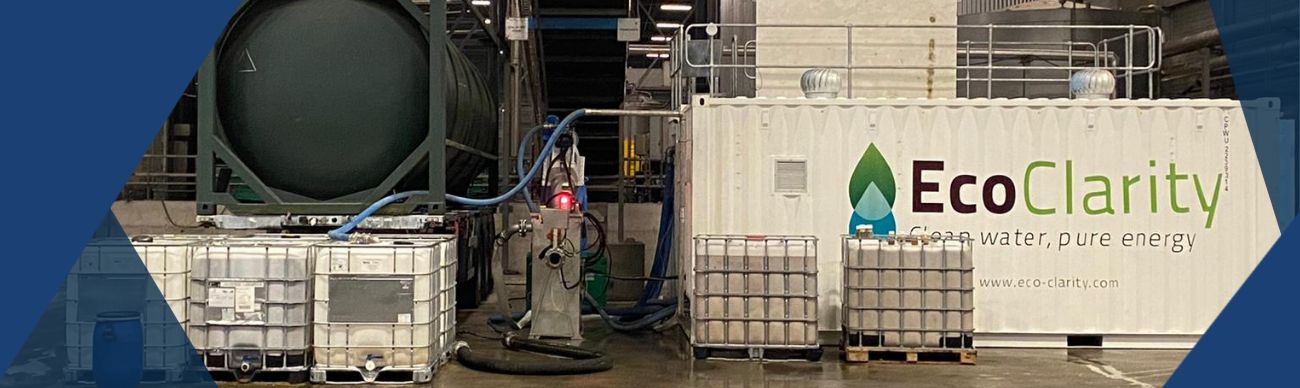
Case Study: The Eco-Clarity Grease Trap Waste Recovery Hubs
At the start of 2020 Fabrinox was approached by UK based company Eco Clarity, a waste to energy service provider, to provide turn-key project services for the co-development and manufacturing of revolutionary “FOG Consolidation Hubs” that are modular, scalable and containerized. These groundbreaking hubs are used for the recovery of Fats, Oils and Grease (FOG) generated by Food Service Establishments (FSE’s).
For this ground-breaking project Eco Clarity has recently been awarded the Project of the Year award in Sustainability at the Sassda & Columbus Stainless Awards, while Fabrinox took home the Project of the Year award in Austenitic Stainless Steel.
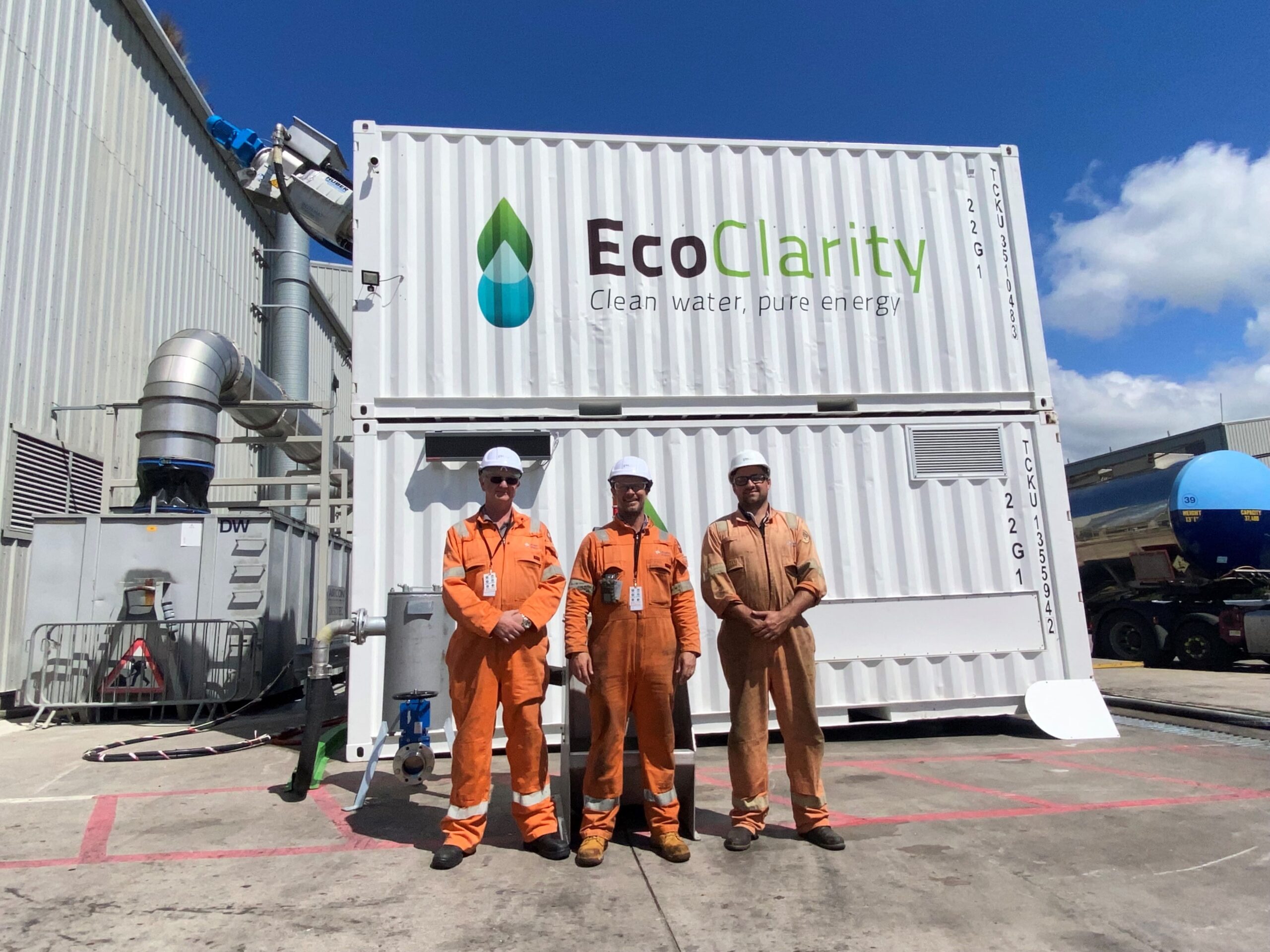
Eco Clarity’s FOG Consolidation Hubs provide accessible disposal locations for haulers to sustainably dispose of FOG containing wastewater before it enters the sewer network or wastewater treatment works, where it can be a major cause of blockages, spills and reactive and costly clean-up operations. These hubs are able to consolidate the FOG present in this waste into a feedstock suitable for Bio Diesel production, which is then blended with the diesel. This enables FSE’s, Haulers and Water Utilities who use Eco Clarity’s FOG Consolidation Hubs for disposal of their waste, the ability to create a circular economy, by running their diesel cars and trucks on the waste that they generate. Ultimately creating value for a valueless product while saving costs, water, transportation and the environment.
What makes the Eco Clarity Fog Consolidation Hubs unique?
An Innovative Approach:
Fabrinox used our expertise in manufacturing and product development to assist Eco Clarity with manufacturing design building and commissioning new FOG recovery technology that is innovative and unique in terms of the systems energy management that renders the process very energy and cost-effective.
We assisted in developing a waste separation system using no settling or other chemicals to successfully separate fat, oils and grease from water. This separation is of such a high quality that the water retrieved is suitable for final water treatment and the fats ready for processing into biofuel.
The manufacturing design allows for circular economy features such as recycling, repurposing, deployment flexibility, and cost-effective material-grade application. The design requires low maintenance and has a very low life cycle cost.
Competitive Life Cycle Costs:
The plant is designed to have a maximum lifespan at minimum initial and operational costs in order to deliver a favorable life cycle cost analysis. For this reason, the material selection for the various elements in the plant is based on material that is most suitable and cost-effective.
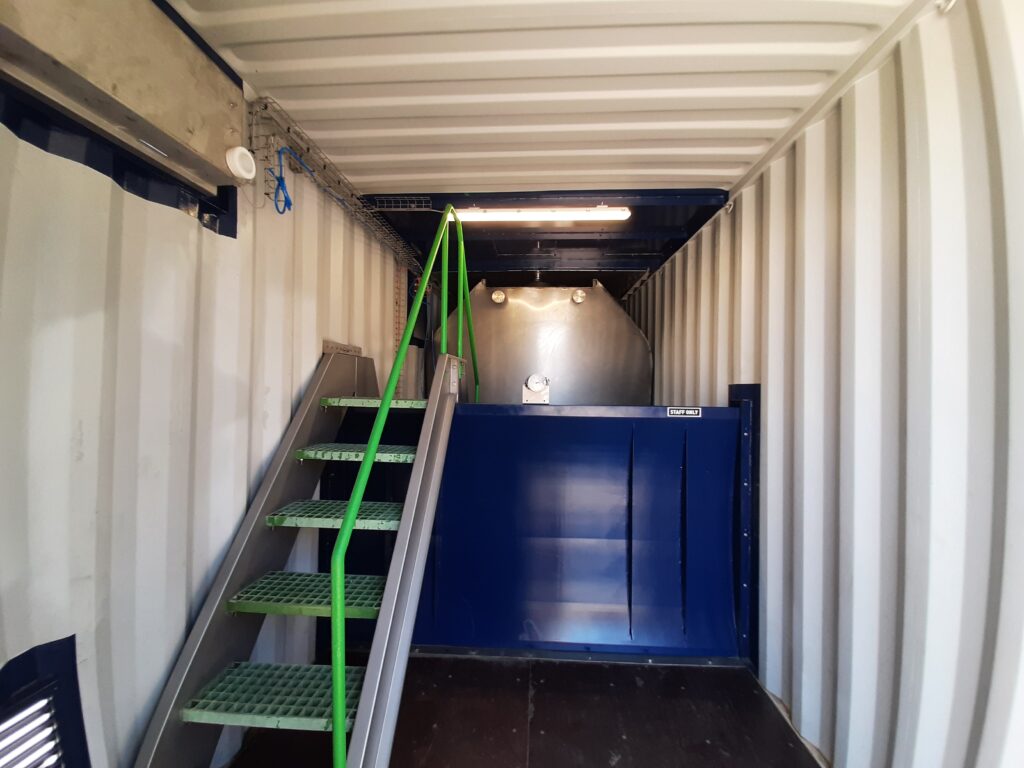
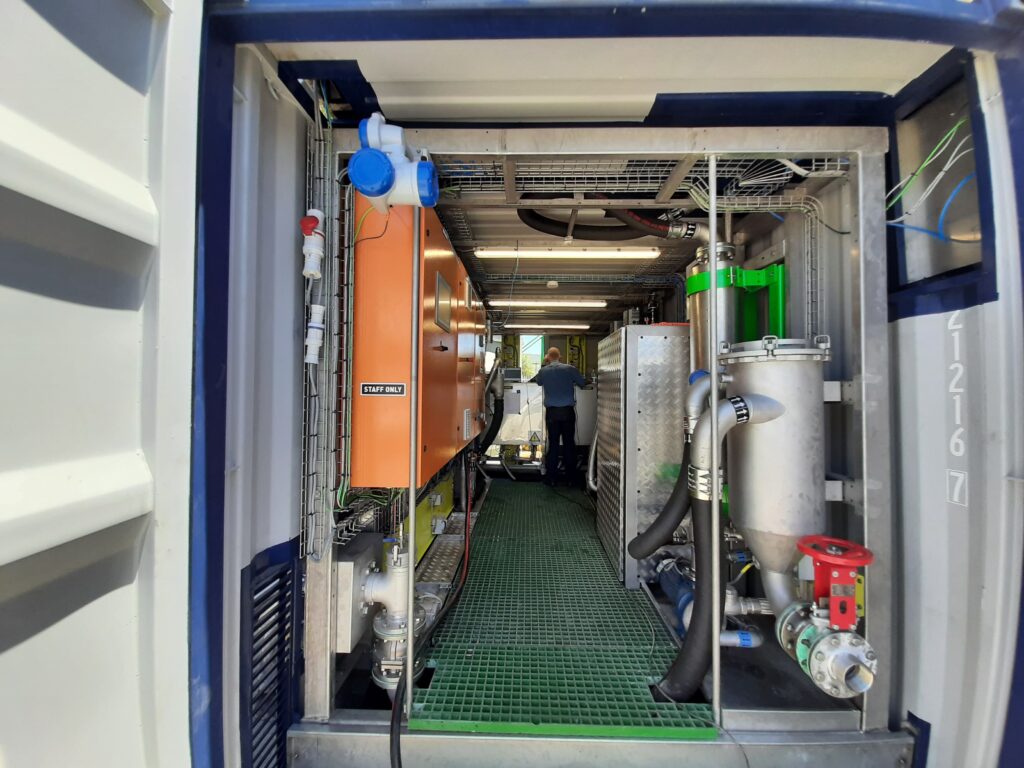
Localisation potential:
The product has huge potential for localisation since the technology is still new to the South African landscape. All the plants in use exist in the UK and Europe with good demand in the market. Whilst this technology is also still new in the rest of the world, legislation and regulation regarding waste disposal, environmental impact and carbon emission control will drive the demand for the product in the developed world. South Africa has good legislation to this effect and increased future enforcement of this legislation will create local demand. In the case of South Africa, the importance of the water retrieval in the process will be a key driver in future.
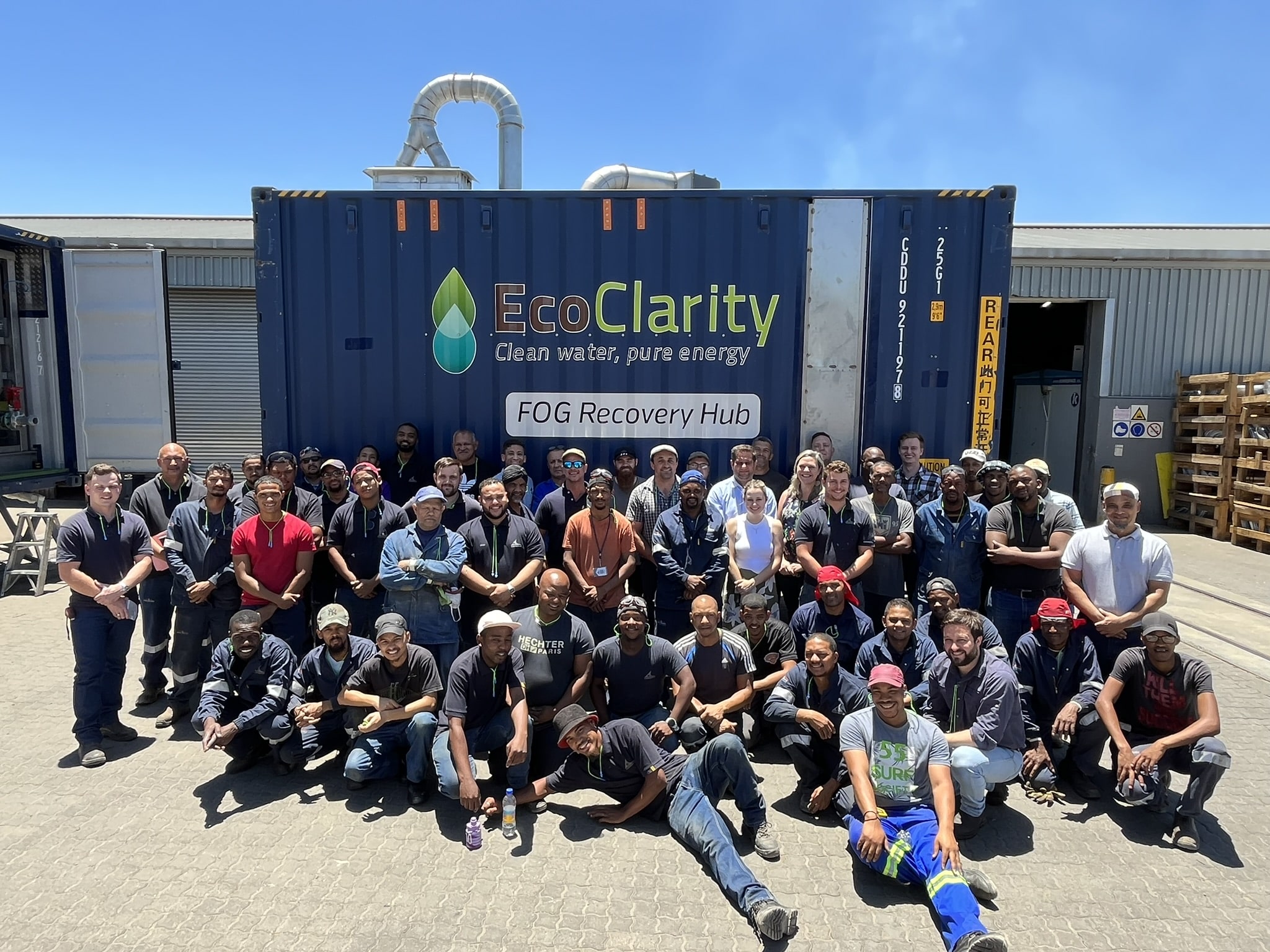
All the developmental protypes and functional units are 100% locally fabricated by Fabrinox with 100% local content except for the repurposed shipping containers and driven equipment such as electrical motors, instrumentation and some fittings not available locally.
The plants create meaningful jobs, especially in the South African stainless steel fabrication as well as at the points of installation. With the increasing demand for these plants, the continued production will increase job creation in the fabrication sector in South Africa since the intent is to keep the global manufacturing of the plants in the South African industry.
Market growth potential:
The fact that the plants are fabricated in South Africa and in use in Europe and the UK offers unique marketing advantages. The local build has created awareness and interest since Fabrinox has invested in hosting open days to display and explain the technology. The claims made by this new technology is tested under stringent European conditions providing a good track record. As mentioned above, the demand for the units will be driven by South African and global legislation and regulations regarding waste disposal, environmental impact and carbon emission control.
As such the local and global market opportunities appear to be strong. As is the current situation, exports of the units will most likely exceed the local demand in the short to medium term.
Functionality:
All restaurants, cafeterias, fast food outlets, industrial kitchens etc., and filling stations are required by law to incorporate grease traps into their wastewater systems as a measure to stop FOG from entering the downstream sewer system and wastewater treatment plant. FOG is collected in grease traps, which must be cleaned regularly to avoid overflowing into the downstream sewer network. This waste is collected by hauliers and is referred to as Grease Trap Waste (GTW). The FOG Consolidation Hubs can accept and process large volumes of GTW in real-time and not in batch form as is the case with traditional methods of disposal. In a network of convenient GTW Consolidation sites, time and logistic costs for GTW haulers can be reduced.
The following should be considered when looking at the plant functionality:
- It will reduce reliance on landfill, enabling efficient, cost-effective disposal of FOG waste at more easily accessible sites.
- Easier and closer access to treatment sites will reduce road use of FOG haulers which results in a positive impact on traffic conditions, road wear and environmental impact.
- The automated and energy-efficiency enables users to screen and separate FOG and organic solids from wastewater before it enters water treatment works, thus reducing downstream water treatment cost as well as the environmental impact in the case of spillage or illegal dumping.
- It is a clean technology with a small footprint in terms of plant size and environmental disruption making it suitable for installation close to activities generating FOG and residential areas. Eco Clarity’s Hubs have a small footprint of 10m2, made up of an automated Huber solids screen, two 6m treatment containers, and a 6m FOG post processing and storage container.
- Throughput time has been drastically shortened from the traditional treatment plants, and the operation can be described as a “drive through” facility for haulers, lower waiting time and traffic congestion at the treatment sites. A standard Eco Clarity GTW Hub, is capable of accepting 10 tons of GTW in 10 minutes, with a further 10 ton truck each 15-20 minutes thereafter. Being automated the system is able to receive waste 24/7.
- The plants are transportable and can therefore be relocated with ease if required. With a quick setup, the Eco Clarity GTW Conversion Hub can be ready to process waste within three days of delivery.
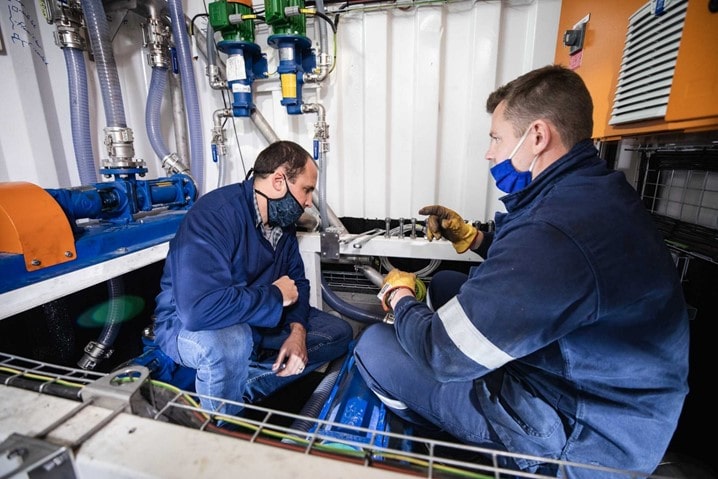
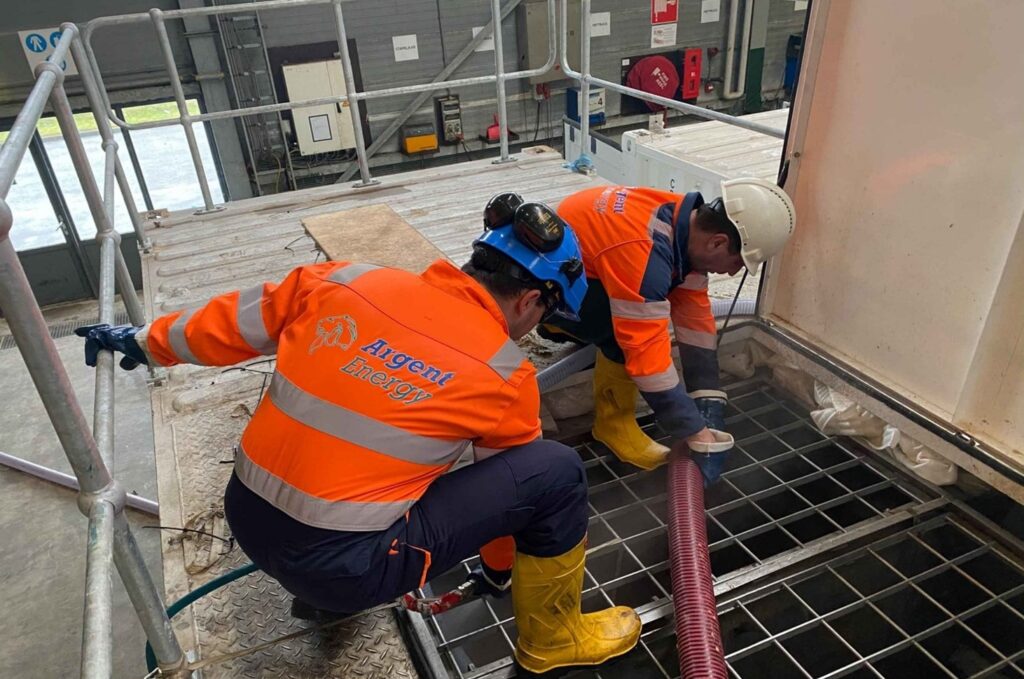
Designed for recyling
Conceptual design:
The technology is developed and designed to recycle highly problematic waste products into environmentally friendly fuel and water. Both fuel and water are critical aspects of environmental protection and the survival of humankind. The technology can consolidate the FOG present in waste into a feedstock suitable for Biodiesel production, which is then blended with the diesel available at service stations. This enables FSE’s, and other users of the technology to create a circular economy, by running their diesel cars and trucks on the waste treated.
Manufacturing design:
Care is taken during fabrication to make use of materials in a way that contributes to recycling and a circular economy. The shipping containers used to house the technology are repurposed used containers, larger stainless steel sheet off cuts from general production activities are used for transportation cladding. More than 60% of the weight of the plant is from stainless steel which is 100% recyclable. The shipping containers can be repurposed for a second time after the plant has reached the end of life or recycled as part of the stainless steel production process.
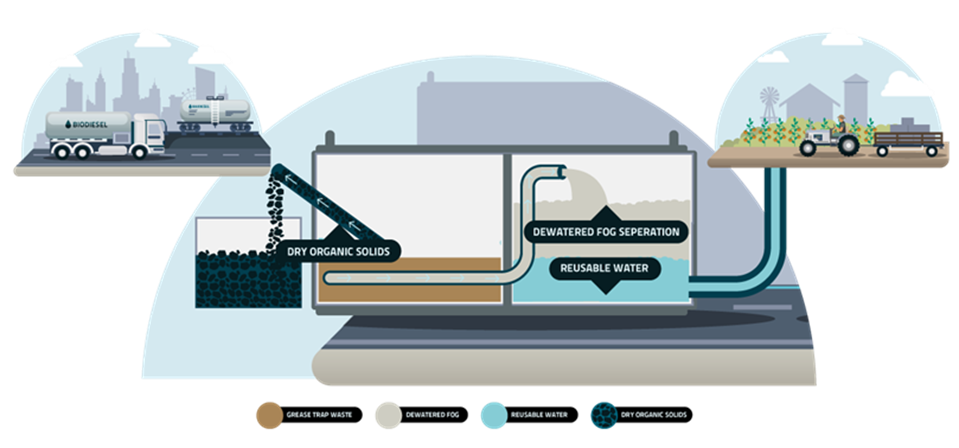
A Positive & Environmental Impact
This technology will have a positive impact on both the environment and general society.
Environmental impact:
Waste and the responsible disposal of it is a major issue in environmental protection. Waste disposal facilities and landfills have been controversial topics when it comes to battling damage to especially water resources. This system enables FOG to be separated before it enters the water system, preventing any contamination and problems. The cleaned water is then reused or safely returned to the waste stream.
The use of fossil fuels is a critical discussion point in terms of climate change and environmental protection. The successfully separated FOG becomes a sustainable raw material that can be used to produce second-generation biodiesel – feedstock for energy recovery in the UK and EU, which qualifies for triple counting renewable energy directive (RED) credits. The oil recovered goes up from 5% to +95% concentration after going through the Eco Clarity system, turning it into a valuable raw material for biodiesel production.
Social impact:
Any technology furthering the cause against environmental impact, advancing a circular economy and contributing to the supply of non-fossil fuels can be regarded as having a positive impact on society.
- A cleaner environment will contribute to general population health and a better social environment.
- Limiting the use of fossil fuels and acting as a source for alternative energy sources contributes to mitigating the impact of humans on climate change thus ensuring a more sustainable future for society.
- The technology can enable the creation of meaningful jobs especially.
- The plants are manufactured in South Africa for the global market. The uptake in the demand for these systems will lead to new technology development and job creation within the South African stainless steel industry. Local demand for the technology can ramp up this potential.
- Through these levels of positive impact, this technology can benefit the economy leading to a better life for all.
Contact us today at sales@fabrinox.com to find out how our team of experts can help you bring your innovative concepts to life.